The ambient temperature measured by the temperature sensors around the FPGAs can be written to the data stream with the status trigger. This information can be used during the ofline analysis to monitor the change in the temperature since the last TDC calibration.
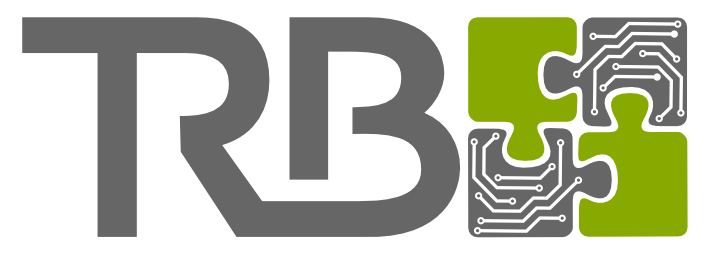
Thanks to the effort of Jennifer Wettig (Universität Mainz), the TRB collaboration now has its own logo, containing puzzle pieces as a symbol for all our different components of software and hardware playing together to form an extensive data acquisition environment.
Most endpoint designs need some configuration bits being programmed after the FPGA has been initialized. Usually these settings depend on the use of the design or specific hardware (e.g. thresholds) and can not be hard coded in the design itself. Now there is the option to store register settings in a separate section of the on-board Flash ROM - all user registers (addresses above 0x8000) can be stored there and can be loaded automatically after a reload of the FPGA design. This can be used e.g. to power cycle an FPGA without requiring interaction from some software and have it back in operation after about 1.5s (ECP3-150, using latest media interfaces) or within milliseconds like the Padwia-FPGA.
In general, this feature is available for all TRB3 and TRB3sc designs, but at the moment is implemented on special request only. One caveat to note: The registers configuration file needs to be prepared by hand and is not generated automatically.
The CBM-TOF board - a 32 channel TDC with optical link, high-quality clock input, low-noise power supply for best TDC performance. The board is fully compatible to TRB3 (it contains a full TrbNet endpoint).
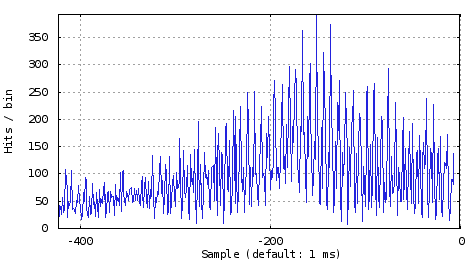
Most designs feature input monitors. The basic functionality is an edge counter monitoring each input channel individually - if read out e.g. once per second one can easily display the rate of input pulses. Besides that there is a high-resolution mode available: One input channel can be selected and the counter be sampled with a given period, down to 100 ns per sample. A buffer stores up to 1000 samples that can be read out subsequently for detailed rate analysis, for example to check micro-structures of the spill or to see if hits close to each other deteriorate the detector performance.